
The Problem
Robotic assisted surgery has revolutionized medical interventions, offering enhanced precision and minimally invasive procedures. However, challenges persist in developing teleoperated manipulators capable of accurately replicating real-time positions from haptic devices. This project aims to address this by designing a 2-degree-of-freedom manipulator that seamlessly interprets position commands via a USB port, potentially advancing surgical capabilities and improving patient outcomes.
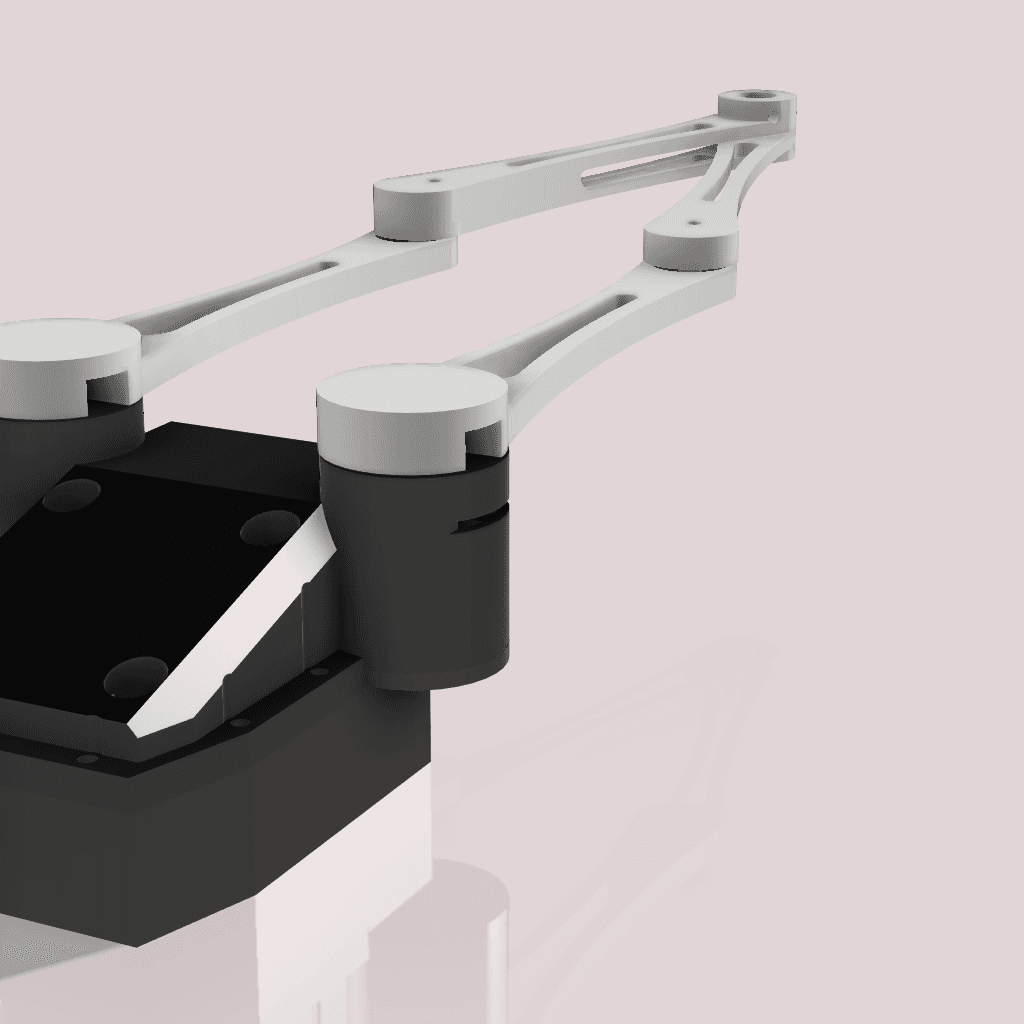
Proposed solution
To address the challenges in developing a teleoperated manipulator for surgical applications, a simple hardware solution is proposed due to the limited time frame. The manipulator design incorporates essential components such as links, joints, and an end effector, ensuring flexibility and precision in performing surgical tasks. Each link and joint is carefully configured to establish the necessary degrees of freedom for optimal maneuverability. All the parts shown above were designed with modularity in mind and 3d printed. This allowed us to 3d print smaller sections of the robot at once, and reprint only parts that were broken or unfit.

Actuators, specifically electrical DC motors, were selected to translate electrical signals into desired mechanical actions, offering the required torque and speed control for our proof of concept. Finally, a microcontroller, the Arduino Nano board, served as the central processing unit, facilitating communication between the sensors, actuators, and external input devices like haptic interfaces. This proposed hardware solution aimed to provide a robust foundation for the development of a teleoperated surgical manipulator capable of accurately executing real-time commands and enhancing surgical outcomes.
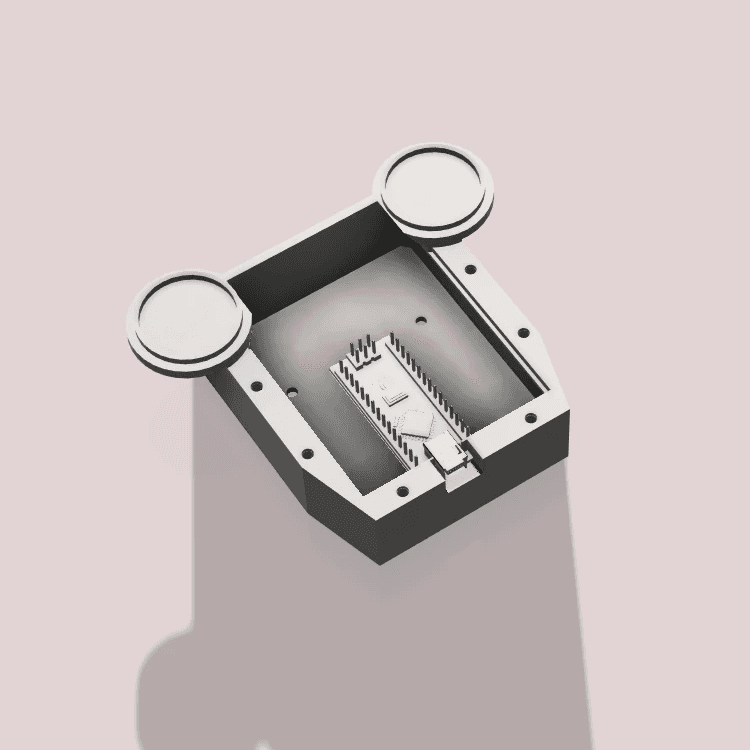
For testing and the demonstration, we ensured the robot's consistency by crafting a custom PCB meticulously soldering all electrical components. Although not obligatory, this step proved pivotal, significantly enhancing the consistency of our results. Moreover, pins connectors were added to improve the ease of replacing a motor if required. This allowed us to present a robot that reflected the though process put behind the final product.
Finally, we were able to sucessfly demo the robot by connecting it to a haptic device. The robots links moved as expected, allowing us to move on a xy plane following the path of the haptic device.
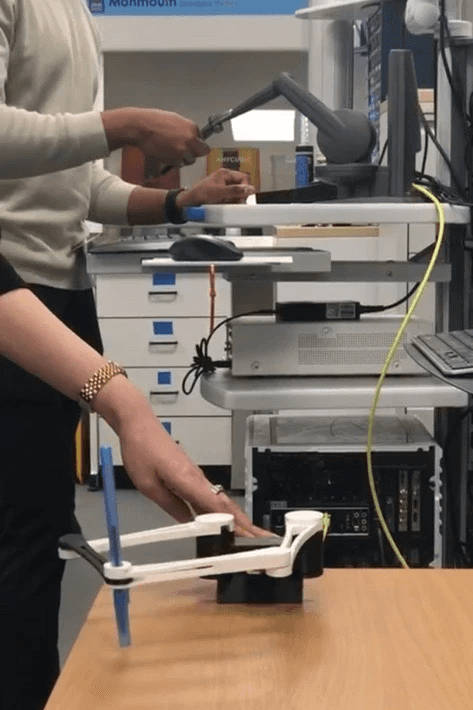